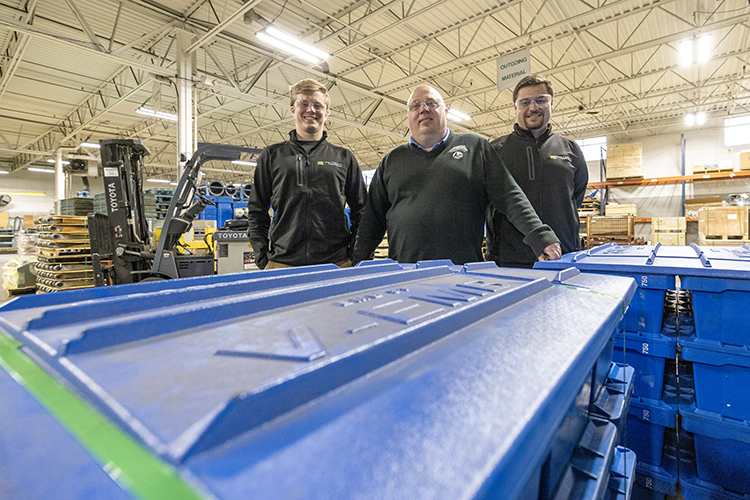
Easton Dobson (left) and Colin Haagensen flank Steve Coolidge, general manager of AAA Sales & Engineering on the floor of the company’s Oak Creek plant. Dobson, Haagensen and another student, Ryan O’Day, worked on a project that benefited the company and gave the students real-world experience. (UWM Photo/Troye Fox)
The three UWM senior engineering students stood on the workroom floor of a Wisconsin manufacturing company, about to tell 70 older, experienced machinists how to improve their inventory system.
Easton Dobson, Colin Haagensen and Ryan O’Day promised their audience that the idea they were about to hear — an idea that originated with management and was engineered by the students — would make their jobs easier.
“We had made sure along the way to get the perspective of the machinists,” said O’Day, who graduated in December 2022 with an undergraduate degree in industrial engineering. “We wanted to hear what was really happening on the floor.”
It went well. So well that the company — Oak Creek-based AAA Sales & Engineering (AAASE) — adopted the students’ proposed solution: a bar-coding system they simply called the Inventory Traceability Project.
Steve Coolidge, AAASE’s general manager, estimates the Inventory Traceability Project will save the company $840,000 annually. As promised by the UWM students, it has already made the machinists’ jobs easier by significantly reducing the time it takes them to locate parts in the 80,000-square-foot building.
62-minute search for parts
AAASE provides precision machined castings and forgings for 13 clients – including Caterpillar and Eaton – and maintains about 400 active part numbers at any time. Hundreds of times daily, machinists must locate these parts, searches that had ranged from one to 62 minutes.
Sometimes, Coolidge said, machinists just gave up the search and sought out a supervisor.
“We had no formal inventory system,” he said. “The only system we had was institutional knowledge. This worked for the tenured workforce, but as new employees joined us, it became a problem.”
Which is why Coolidge sought help from UWM’s Department of Industrial & Manufacturing Engineering, housed in the College of Engineering & Applied Science. It was the first time AAASE worked with UWM.
‘Applying what you learn’
Through a senior design class for industrial and manufacturing engineering students, AAASE challenged the team of Dobson, Haagensen and O’Day to create a method to record and maintain the physical location of $2 million worth of parts that ranged in price from $17 to $1,400 each. In this mandatory class, students work on teams as they transfer their classroom knowledge to real-world industrial problems.
“Academics are important, but applying what you learn in the classroom to business is fundamental,” said O’Day, who will pursue a master’s degree in data science in fall 2023 at the University of Denver. “We were tasked with a sizeable project from an actual client, and it was very valuable.”
Coolidge mentored the student team over the three-month project. They were advised by Dah-Chuan Gong, a UWM visiting scientist who is a supply chain and logistics expert, and Wilkistar Otieno, associate professor and chair, industrial and manufacturing engineering.
Industrial engineering students learn how to make things better in any industry by analyzing and optimizing the integration of people, machines, materials, time and other resources.
“Industry-driven, senior design projects give our students an incomparable way to learn and grow,” Gong said. “In the process, they face current, real-world industrial problems. To succeed, they must learn more carefully how to define scope, how to apply appropriate methodology, and how to measure and justify their results.”
Benefits accrue as company rolls out students’ system
Today on the workroom floor at AAASE, machinists are using the Inventory Traceability Project to easily locate parts. The average search time for a part has decreased from 11 minutes to less than three, which means the company’s 46 machines are idling 3,500 fewer hours each year. Human error from manual data entry has been reduced, and the process of identifying parts and transferring information has been streamlined.
There will be more to come. The students set up the system so the company could roll it out incrementally.
“The student team did an amazing job of working with our employees,” Coolidge said. “They brought a passion for making their work easier and more efficient, and our team immediately respected them for that.”
Previous project
This isn’t the first time that engineering students helped a company solve a problem. Last year, another group of students created a system that saved a Saukville specialty steel manufacturer more than $40,000.
“The students knocked it out of the park,” said Ted Fitzpatrick, a process metallurgist at Charter Steel and the team’s contact at the company. “The entire reason we changed the heat-treatment cycle was because of the work the student group did. They took it above and beyond.”
Written by Carolyn Bucior
Link to original story: https://uwm.edu/news/uwm-engineering-students-create-solution-that-saves-company-840000-per-year/